Water pumps play a crucial role in managing water supply, heating, and sewage systems. They are extensively used for the forced pumping of liquid mediums in both industrial and domestic settings. Among the various types of pumping equipment, centrifugal pumps are the most prevalent due to their efficiency and versatility. This article delves into the intricacies of centrifugal pumps, their working principles, applications, classifications, advantages, disadvantages, and leading manufacturers, as well as the importance of pump repair services to maintain their optimal performance.
What is a Centrifugal Pump?
A centrifugal pump is a mechanical device designed to move fluids by converting rotational kinetic energy to hydrodynamic energy. This conversion is achieved through a rotating impeller, which accelerates the fluid outward from the pump’s central point, creating a centrifugal force that pushes the liquid through the pump system.
Working Principles of Centrifugal Pumps
- Fluid Entry: Fluid enters the pump through the eye of the impeller, located at the center.
- Acceleration: As the impeller rotates, it accelerates the fluid outward radially.
- Kinetic to Hydrodynamic Energy: The impeller’s kinetic energy converts to hydrodynamic energy, increasing the fluid’s velocity and pressure.
- Discharge: The fluid is directed to the pump’s discharge outlet, where it exits at a higher pressure.
Centrifugal pumps are known for their simplicity and efficiency. They have fewer moving parts compared to other types of pumps, which translates to lower maintenance costs and longer operational life. Their design allows for a smooth flow of liquid, minimizing turbulence and energy loss, which contributes to their high efficiency.
Applications of Centrifugal Pumps
– Heating Systems: Circulating coolant in centralized and autonomous heating systems. They ensure the even distribution of heat in buildings, enhancing energy efficiency and comfort.
– Water Supply: Providing water to residential, commercial, and industrial properties. They are used in municipal water supply systems, ensuring a consistent and reliable water supply.
– Wastewater Management: Transporting wastewater to sewer systems. They play a vital role in sewage treatment plants, helping to move wastewater through different stages of treatment.
– Irrigation Systems: Organizing irrigation and watering agricultural sections. They ensure the efficient distribution of water to crops, enhancing agricultural productivity.
– Oil and Gas Industry: Pumping oil and oil products on an industrial scale. They are used in various stages of oil extraction and refining, ensuring the smooth flow of oil products.
Classification of Centrifugal Pumps
– Number of Working Wheels:
– Single-Stage (Single-Wheeled): Consists of one impeller. Suitable for low-pressure applications.
– Multi-Stage (Multi-Wheeled): Contains multiple impellers for higher pressure. Used in applications requiring high pressure and long-distance fluid transfer.
– Method of Water Drainage:
– Simple: Without a guide device. These are the most basic form of centrifugal pumps.
– Turbine Wires: With guide vanes to direct fluid flow. These pumps offer improved efficiency and are used in more complex applications.
– Type of Water Supply:
– One-Sided Supply: Fluid enters from one side. Commonly used in simple, low-pressure systems.
– Bilateral Supply: Fluid enters from both sides. Suitable for high-pressure and high-flow applications.
– Developed Pressure:
– Low-Pressure: Up to 20 meters. Used in applications where only a small lift is required.
– Medium-Pressure: 20 to 60 meters. Suitable for general water supply and irrigation systems.
– High-Pressure: More than 60 meters. Used in high-pressure systems such as firefighting and industrial processes.
– Shaft Orientation:
– Horizontal Shaft: Shaft positioned horizontally. These pumps are easier to install and maintain.
– Vertical Shaft: Shaft positioned vertically. These pumps are used where space is limited and in deep well applications.
– Nature of the Pumped Fluid:
– Water: General water use. Suitable for clean water applications.
– Fecal: For sewage. Designed to handle solid-laden wastewater.
– Groundwater, Sand, Mud, Acid: Specialized fluids. These pumps are built to handle abrasive and corrosive fluids.
– Purpose:
– General Purpose: Standard applications. Used in everyday water supply and heating systems.
– Mine, Artesian: For specific uses like wells. These pumps are designed for high-lift and high-pressure applications.
Industries Using Centrifugal Pumps
– Oil and Gas: Pumping oil products, sludge, and mud. They are used in extraction, refining, and transportation processes.
– Industrial and Fire Protection: Heating, ventilation, boiler systems, air conditioning, fire sprinkler systems. They ensure efficient heating, cooling, and fire safety in industrial plants.
– Waste Management and Agriculture: Wastewater disposal, drainage, irrigation, flood protection. They help manage waste and ensure efficient water use in agriculture.
– Pharmaceutical, Chemical, and Food Industry: Pumping paints, hydrocarbons, cellulose, food, and beverages. They are used in manufacturing processes, ensuring the safe and efficient handling of various fluids.
Advantages of Centrifugal Pumps
– High Efficiency: Effective in converting energy. They provide high flow rates and are energy-efficient.
– Consistent Flow Characteristics: Maintains stable speed and pressure. They ensure a steady and reliable flow of fluids.
– Compact Size: Relatively small dimensions and weight. They save space and are easy to install.
– Simple Design: Allows direct connection with a drive engine. This reduces the need for additional components and simplifies maintenance.
– Low Failure Rate: Fewer overloaded components. They are durable and have a long operational life.
Disadvantages of Centrifugal Pumps
– Priming Requirement: Must be filled with liquid before operation. This can be a limitation in applications where the pump cannot always be kept full of liquid.
– Gas Sensitivity: Prone to flow interruption if gases are present in the fluid. This can lead to inefficiencies and operational issues.
– Impurity Sensitivity: Less effective with impure fluids unless specialized. Standard centrifugal pumps can be damaged by abrasive or corrosive fluids.
– Maintenance Needs: Regular upkeep and replacement of wear elements. This requires ongoing investment in maintenance and spare parts.
Leading Manufacturers of Centrifugal Pumps
– Grundfos (Denmark): Known for circulation pumps for heating and air conditioning, as well as industrial applications. They are a global leader in advanced pump solutions and water technology.
– Wilo (Germany): Specializes in pumps for water supply, heating, ventilation, and air conditioning. They are known for their innovative solutions and energy-efficient products.
– Pedrollo (Italy): Produces a wide range of pumps, with a production capacity of 2 million units annually. Their products are sold in over 160 countries.
– Calpeda (Italy): Established manufacturer of diverse pumping equipment. They offer a wide range of pumps for various applications.
– Aquario (Russia): Russian brand known for robust pumping solutions. They provide reliable and cost-effective pumps for different uses.
– Karcher (Germany): Produces a variety of centrifugal pumps. They are well-known for their high-quality and durable products.
– Jiglex (Russia): Manufacturer of household pumps and high-quality water supply equipment. They focus on delivering efficient and reliable solutions for domestic water supply.
Conclusion
Centrifugal pumps are integral to numerous applications, from household water supply to industrial processes. Their efficiency, versatility, and reliability make them indispensable in modern infrastructure. Understanding their principles, classifications, applications, and the leading manufacturers helps in making informed decisions for selecting the right centrifugal pump for specific needs.
By leveraging the advantages and addressing the limitations of centrifugal pumps, industries can optimize their fluid handling processes, ensuring operational efficiency and cost-effectiveness. As technology advances, the development of more specialized and high-performance centrifugal pumps will continue to support a wide range of applications, further solidifying their role in modern engineering and industry.
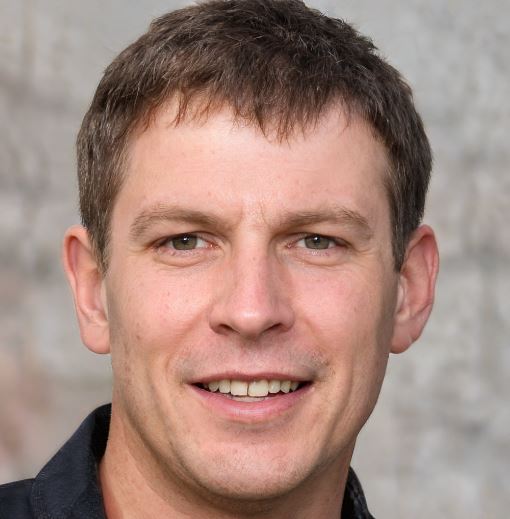
Hockey fan, nature enthusiast, music blogger, vintage furniture lover and multidisciplinary designer. Doing at the intersection of art and mathematics to craft experiences that go beyond design.